Innovations in Surface Mount Technology: Flexible Circuits and Conductive Inks
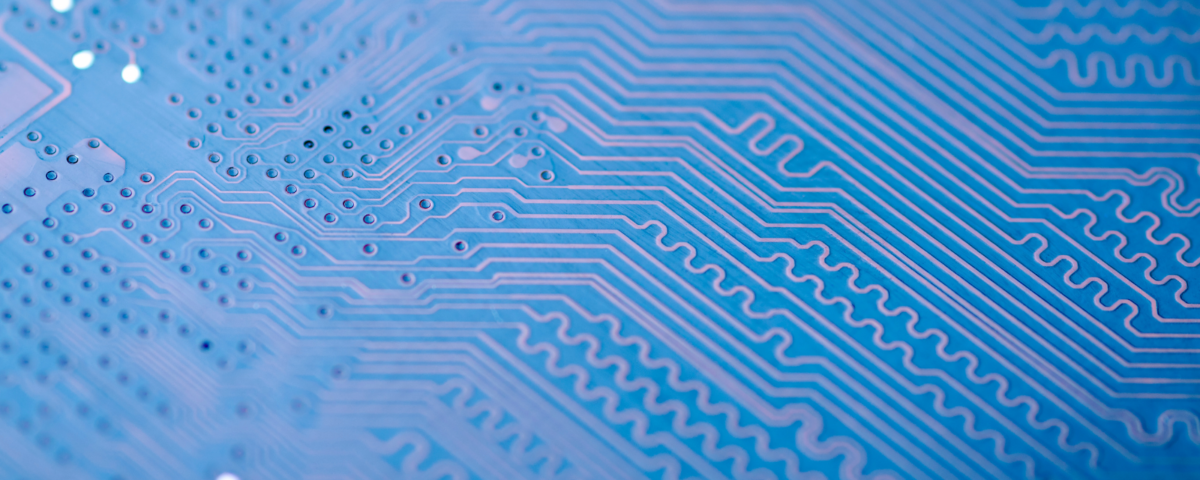
In the world of electronics manufacturing, innovation is key to staying ahead of the competition. One area that has seen significant advancements is surface mount technology (SMT), especially with the increasing reliability of flexible circuits and conductive inks. These technologies are revolutionizing the way electronic devices are designed and manufactured, offering a range of benefits over conventional rigid printed circuit boards (PCBs).
What are Flexible Circuits and Conductive Inks?
Flexible circuits, also known as flex circuits or flexible PCBs, are electronic circuits constructed on flexible, high-temperature resistant substrates such as polyimide. These circuits can be bent, twisted, and shaped to fit into spaces that rigid PCBs cannot, making them ideal for compact and lightweight electronic devices.
Conductive inks are a vital component in the production of flexible circuits. These inks are typically made from silver or carbon particles. Conductive inks are applied to flexible substrates using printing techniques such as screen printing or inkjet printing. Once dried or cured, the ink forms conductive traces that can carry electrical signals between components on the flexible circuit.
Advantages of Flexible Circuits and Conductive Inks in SMT
- Direct Component Soldering: One of the key advantages of flexible circuits is the ability to solder components directly onto the surface mount device (SMD). This eliminates the need for through-hole components and allows for a more compact and lightweight design. Components such as LEDs can be directly soldered onto the flexible circuit, reducing assembly time and costs.
- Enhanced Connector Integration: A key advantage of flexible circuits over their rigid counterparts lies in their ability to streamline the connector integration process. Thanks to their direct-solder capabilities, connectors can be soldered directly onto the circuit traces, bypassing the traditional requirement for specific connector designs. This direct connection method not only simplifies the manufacturing process by eliminating extra steps but also translates into significant time and cost savings.
- Reduced Manufacturing Steps: Flexible circuits can streamline the manufacturing process by eliminating the need for multiple components and assembly steps. With components soldered directly onto the SMD and interconnects soldered directly onto the device, manufacturers can reduce the number of manufacturing steps, resulting in faster production times and lower costs, with added environmental benefits like reduced waste and energy consumption.
- Enhanced Reliability: Flexible circuits offer improved reliability over rigid PCBs, especially in applications where the device is subjected to bending or flexing. Their resilience against mechanical stress means electronic devices last longer and are less prone to failure, an essential factor for wearables, flexible displays, and medical devices.
Surface mount technology using flexible circuits and conductive inks offers a range of benefits over traditional rigid PCBs. From the ability to solder components directly onto the SMD to the freedom in connector design and the reduction in manufacturing steps, these technologies are revolutionizing how electronic devices are designed and manufactured. As the demand for smaller, lighter, and more flexible electronic devices grows, flexible circuits and conductive inks will play an increasingly important role in the future of electronics manufacturing.