What Is Cavitation?
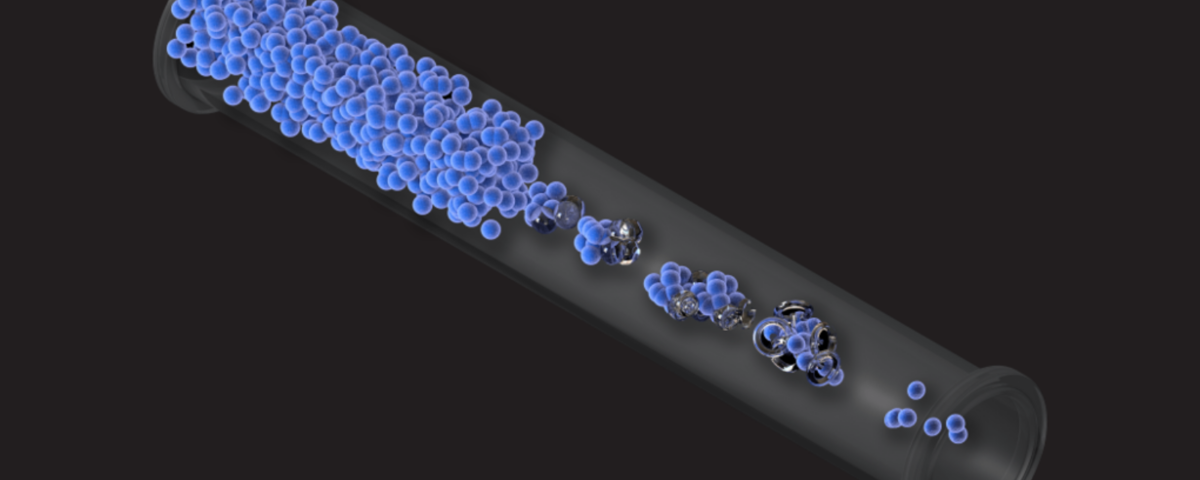
Cavitation is the rapid creation and implosion of vapor bubbles in a liquid. When these spherical vapor bubbles collapse, they form liquid micro-jets focusing energy on extremely localized areas. When vapor bubbles are created and collapsed under the right conditions, they can release a tremendous amount of energy via these jets.
ACI Materials’ patented cavitation process is very efficient at using the energy of cavitation to break apart agglomerated particles and wet out the surface much more effectively than other dispersion processes. We are able to process viscous liquid in continuous phases, such as polymer solutions. These are highly effective at keeping the particles dispersed via robust steric stabilization of the particle surfaces.
Advantages of Cavitation
The cavitation process creates many advantages over other media-less mixing processes, such as three roll mills, when making functional inks and pastes. Unlike these traditional mixing processes, cavitation effectively fully disperses the solid phases of a formulation into the surrounding matrix, greatly improving the mechanical and electrical properties of the resulting material. Other advantages include:
- Superior conductivity
- Improved rheology
- Better mechanical performance
- Unparalleled batch-to-batch consistency
- Easy to apply
- Environmentally friendly
ACI Material’s cavitation process increases conductivity in bulk-mixed materials by 50 to 200 percent. The dispersion process allows for more connective pathways, which leads to higher conductivity.
The elimination of any agglomerates in the materials during cavitation enables finer line printing and more robust, clog-free application. In addition, the cavitation process does not modify particle morphology and the influence of particulate shape on rheology can thus be prescribed.
The inks created through the cavitation process can stretch and flex effortlessly, which makes them ideal for wearable applications. Improved dispersion and elimination of agglomerates obtained with cavitation eliminate the initiation sites that can cause failure at lower stress levels. Improved dispersion also improves fatigue of these materials, especially for stretchable and flexible products, as the solid phase moves more easily and predictably within the polymer matrix. This mitigates the onset of damage within the material as the ink is cycled during use.
This automated process creates greater batch-to-batch consistency without damaging the functional inks. ACI’s cavitated materials have a much tighter distribution of particle sizes than is obtainable with bulk mixing technologies.
The cavitation process yields materials that deposit more smoothly and uniformly, which means applying these materials becomes faster and more consistent. ACI Material’s thermal barrier materials, for example, can be rolled or sprayed onto various substrates and cure at room temperature in less than 24 hours.
ACI’s patented cavitation process takes place in a closed system, so there is no off-gassing of volatile organic compounds (VOCs), as is the case with three roll mills and other bulk mixing technologies. At the end of the workday, when processing stops, ACI’s cavitation equipment remains closed and doesn’t require cleanup. No cleanup is required while processing the same products in the system. This allows for many batches to be made over a period of time without cleaning the machine. ACI’s cavitation process enables the production of high-performance materials with superior properties, which are manufactured without the release of VOCs while saving cleaning materials and diminishing waste. ACI is proud of our clean production process, the benefits to the environment, and the benefits to the performance of our products.